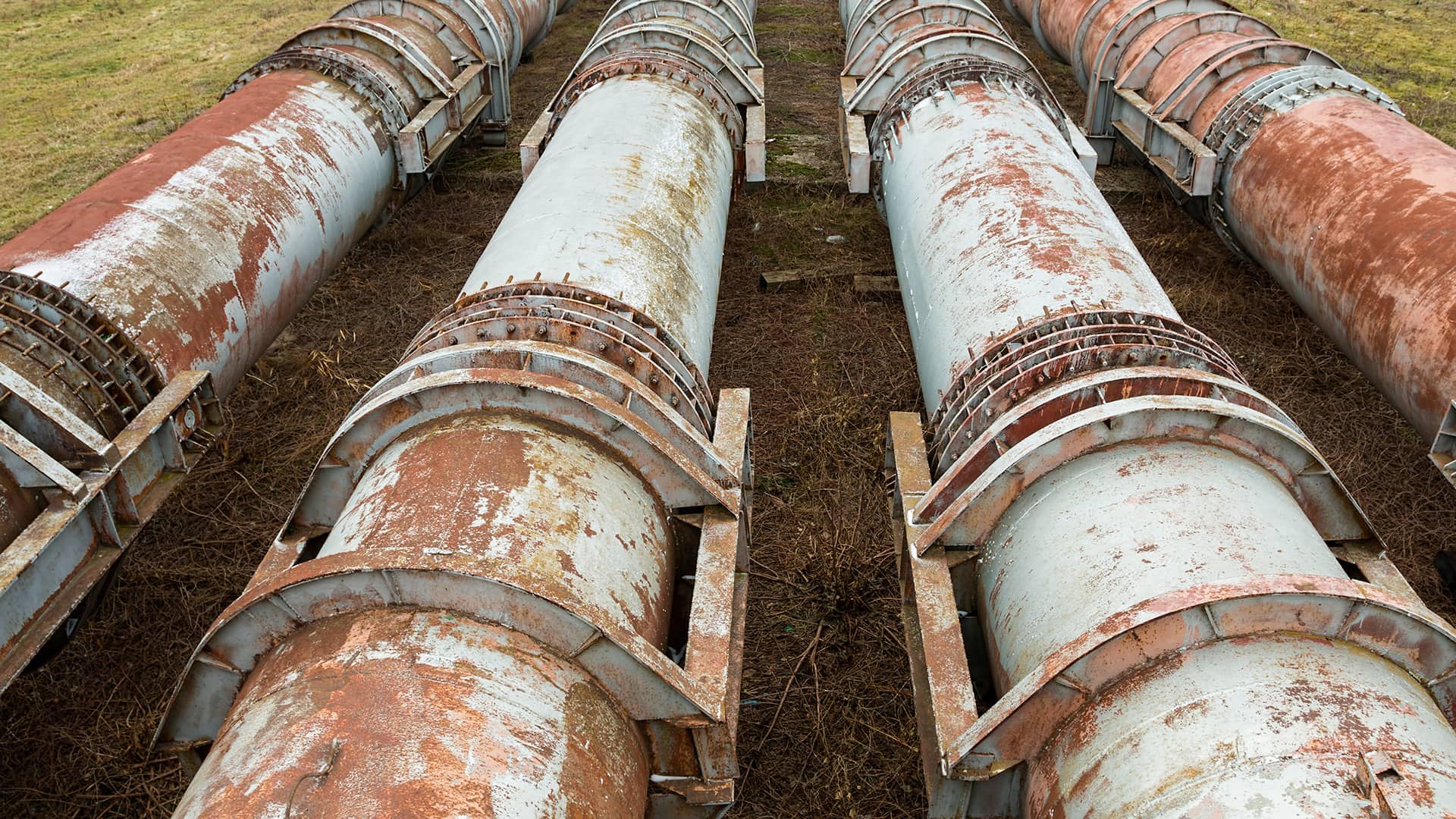
Extracting more natural gas to boost market supply is the most effective solution to bring down rising energy prices. However, once the additional new supply becomes available, getting it to the end customer now becomes priority. There are different options available for moving the gas, but one choice stands above the others for its speed of delivery and low cost – THE PIPELINE.
How fast does natural gas move through a pipeline?
Natural gas usually flows through interstate pipelines at roughly 10–20 mph. Compressor stations placed every 40–100 miles re-pressurize the gas, pushing it forward and keeping its speed—and therefore the overall flow—steady across the network.
Source: Interstate Natural Gas Association of America
Pipelines provide the fastest and cheapest option because the existing infrastructure already connects major cities, storage sites, and energy hubs into a single robust network. To keep the gas moving continuously and uninterrupted requires maintaining the integrity and health of the pipelines in this network. Damage to any segment not only results in huge repair costs but also significant downtime, which cuts off delivery of the gas.
Oxygen entry into pipelines cause damage and can take them offline
Oxygen is the 3rd most abundant element by mass in the universe but, unknown to many, does not exist naturally in gas. While it is critical for life, oxygen is surprisingly a contaminant in pipelines. Within the industry, this is a well-documented problem for natural gas production and transmission. And the problem is not avoiding oxygen concentrations that could support combustion. Instead, it is avoiding oxygen concentrations at much lower levels – specifically, levels measured in the parts per million (PPM).
So what happens when oxygen enters a pipeline? Even trace amounts of the molecule, once inside, will combine with other compounds, including hydrogen sulfide, carbon dioxide and water, to form sulfuric acid and carbonic acid. This destructive mixture will corrode and damage the interior of piping systems over time. At the minimum, the damage can lower the pressurized environment and decrease the speed of gas delivery, requiring segments of the pipeline to go offline for repairs. In a worse-case scenario, more extensive damage can lead to even an explosion at the region of the pipeline. This is something that no one wants, including both the pipeline operator and environmentalist groups, and it is an issue having mutual agreement.
#1 Risk is not an observable pressurized leak BUT AN OXYGEN INGRESS
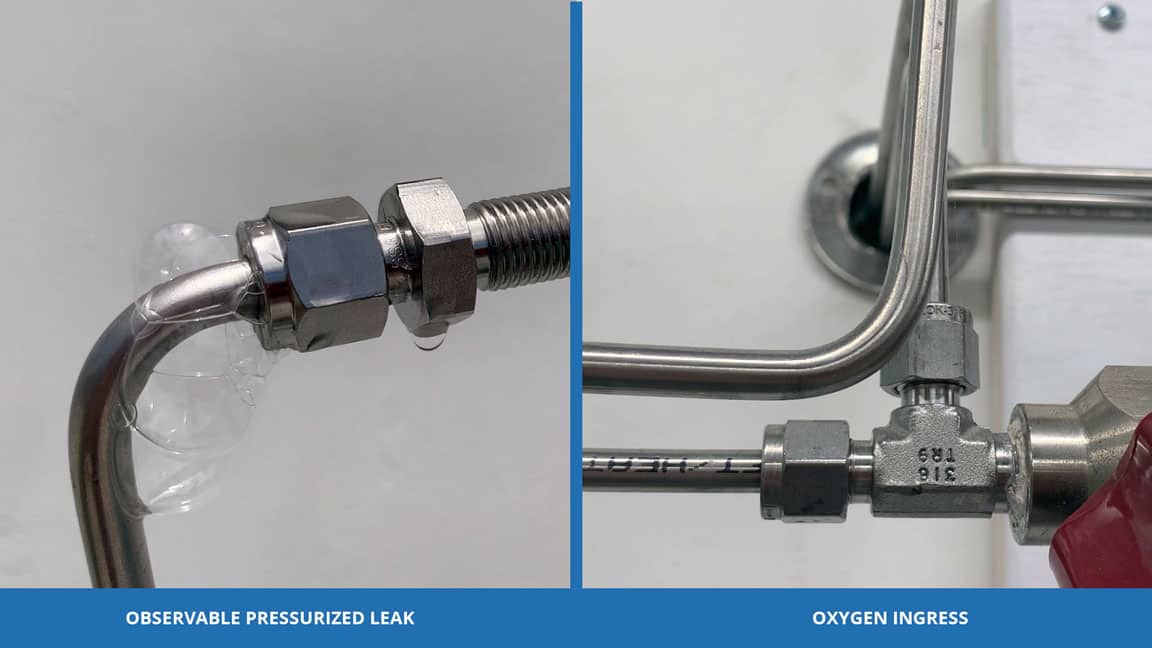
Before we consider how to prevent oxygen from entering the pipeline, it is necessary to understand how it happens. A common misconception is believing oxygen cannot enter a pressurized gas pipeline if there are leak points in the system. Intuition and common sense would assume the gas blowing out of the leak from the pressurized pipeline would push any oxygen molecule away from that leak! Unfortunately, this is only partially true.
Through counter-intuitive, the explanation is found in Dalton's Law of Partial Pressures. The Law states the pressure of each gas exerted in a mixture is the same as would be exerted if a lone gas occupied the container. This means gas molecules flow in both directions if there is an opening, regardless if there is a large observable pressured leak or a small oxygen ingress completely undetectable to the human eye!
It is easier to understand how oxygen enters a pressurized pipeline when we visualize this scenario on a molecular level instead of the gross level normally dealt with by pipeline operators. Gases are not homogeneous, non-compressible fluids but are instead a collection of molecules that are always in motion with large spaces between them. If there is a small leak in a pressurized gas system, there will certainly a large volume of molecules moving from the high-pressure region to the low-pressure area. But there will also be a meaningful amount of gas (ambient air) transferring from the low-pressure region to high-pressure side. Keep in mind the relative size of any leak path is massive when compared to an oxygen molecule.
Trace Oxygen Analyzers are a necessity for pipelines
The leaks posing the most risk to pipelines are the oxygen ingresses that workers cannot see. They are the ones going undetected and unrepaired, and the ones responsible for the formation of corrosive compounds inside the interior of pipelines. It comes as no surprise that tariffs on contractual agreements between two parties set limits on the amount of trace oxygen allowed for transported gas. These limits are incredibly strict, measured in parts per millions, and sometimes even set below 10 PPM.
Protecting the pipeline network starts with installing a Trace Oxygen Analyzer. But it cannot be just any random unit. The Trace Oxygen Analyzer must be capable of delivering fast, accurate measurements in ‘real-time’. Its accuracy must be available in multiple tight output ranges and repeatable under demanding environmental conditions. Pipeline operators should be cognizant of whether a Trace Oxygen Analyzer’s performance specifications meet their exact needs. More importantly, they should evaluate the underlying design or technology to understand whether the Analyzer can deliver on the promise of performance. Because in the end, the proper Trace Oxygen Analyzer does more than monitor the readings of the transported gas, it provides the alert for pipeline maintenance or repairs to ensure the gas keeps flowing uninterrupted.