AMI’s products perform three vital functions
1
Monitoring the oxygen concentration in a heat treatment chamber to verify the atmosphere is optimal for the process and is not too high.
2
Monitoring gas going to the heat treatment process to ensure oxygen levels are not too high.
3
Protecting the worker environment by ensuring adequate levels of oxygen are supplied.
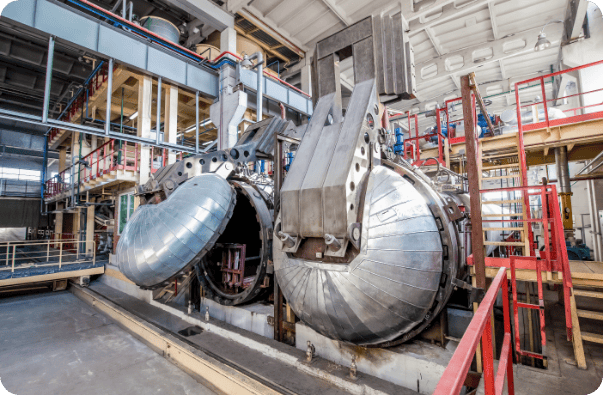
Precision Gas Monitoring
for Heat Treatment Processes
Accurately monitoring atmosphere gases is critical to ensure optimal conditions when treating materials in processes such as annealing, tempering, quenching, and nitriding. Companies typically perform these heat treatment activities using equipment like industrial ovens and furnaces. Conditions inside these devices require strict monitoring to ensure their safe and effective operation.
Companies must obtain the proper gas analyzer for specific heat treatment processes and operational conditions. They may opt for stationary analyzers to monitor treatment processes. A portable solution may make more sense for the qualification, validation, or troubleshooting of equipment or processes.
AMI Products to Monitor the
Heat Treatment Process
AMI manufactures multiple products that provide continuous, real-time data to help optimize the treatment process and enhance the safety of the working environment. We offer trace and percent oxygen analyzers and oxygen deficiency monitors to address your unique requirements.
AMI’s analyzers address multiple issues affecting industrial heat treatment processes.
- Verify the oxygen concentration in the heat treatment chamber to ensure it is optimized for maximum process yields.
- Combustion is enhanced by tuning heat treatment processes based on the data collected by the analyzers.
- Analyze and monitor the environment to protect workers from accidental asphyxiation caused by oxygen deficient environments.
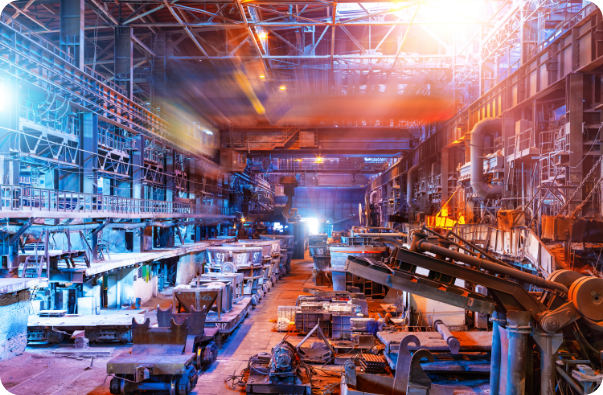
Permanent Mount Analyzers
Permanent mount analyzers are stationary, panel-mounted devices. They monitor the heat treatment environment. For example, the MODEL 2001 family of devices is typically utilized to monitor that O2 maintains optimal composition levels during the actual heat treatment process. The MODEL 70 is often used to verify the existence of safe O2 levels in the treatment oven prior to opening it to the environment.
Trace Oxygen Monitoring
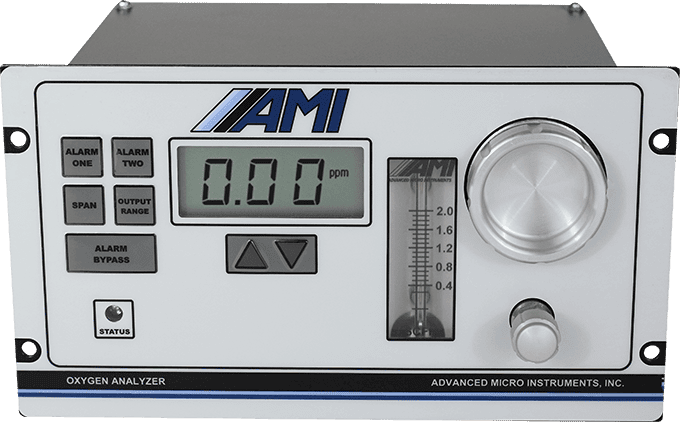
MODEL 2001RS/RSP
Percent Oxygen Monitoring
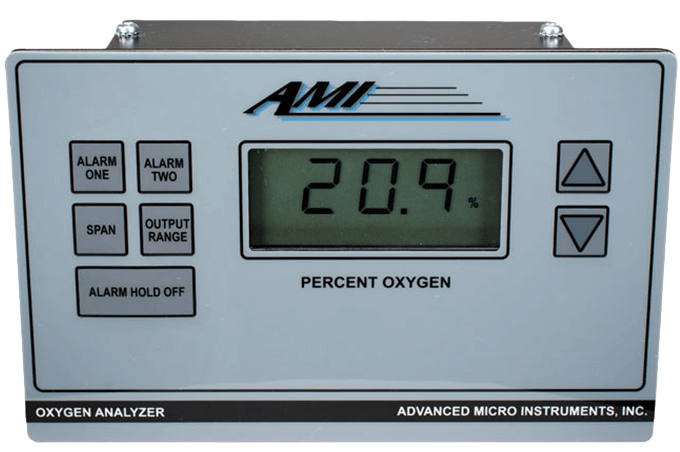
MODEL 70
Oxygen Deficiency Monitors
Oxygen Deficiency Monitors are stationary, panel-mounted devices. They monitor the oxygen levels in the environment and will alarm when oxygen levels are deficient for human safety. They are installed where asphyxiating gases are used and stored.
Oxygen Deficiency
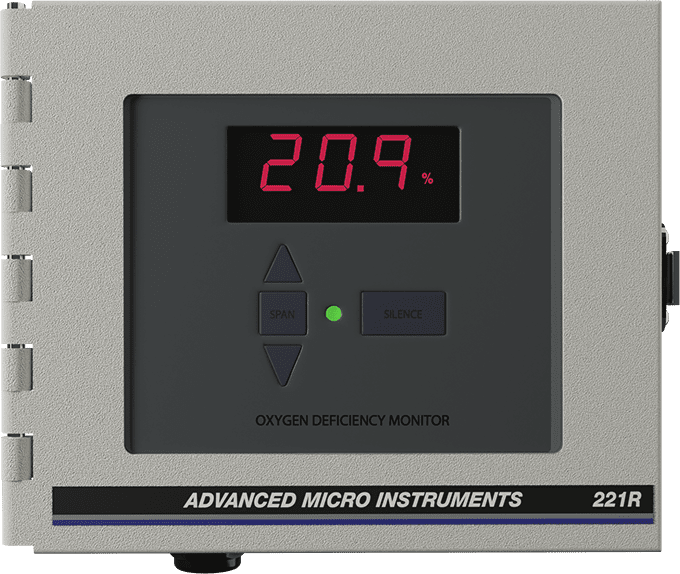
MODEL 221R
Portable Analyzers
Portable oxygen analyzers are designed to address usage scenarios where it is impractical or impossible to deploy a permanent mount analyzer. For example, an operator may need to check oxygen levels at multiple locations that do not have a permanent oxygen analyzer installed. Portable analyzers can also be crucial in furnishing a second reading to verify the accuracy of existing instrumentation.
AMI offers two portable oxygen analyzer models. The MODEL 1000RS is a portable trace oxygen analyzer for use in hazardous areas. It delivers extremely accurate measurements with sensors optimized to identify trace oxygen levels.
The MODEL 111 is a portable and stable percent oxygen analyzer for non-flammable gas samples that provides users with flexibility and versatility to address changing requirements.
Trace Oxygen Monitoring
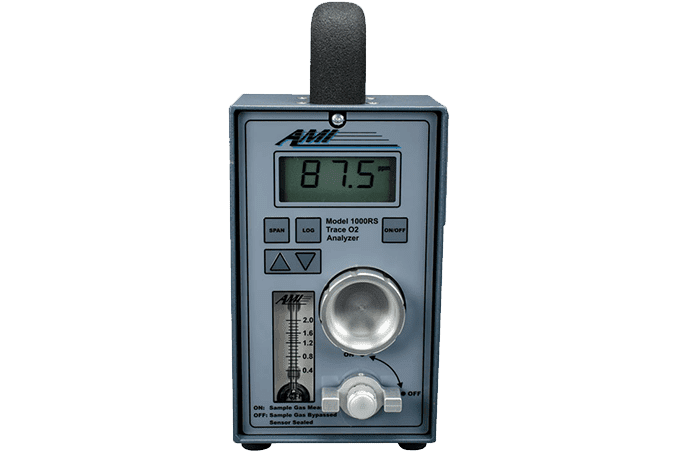
MODEL 1000RS
Percent Oxygen Monitoring
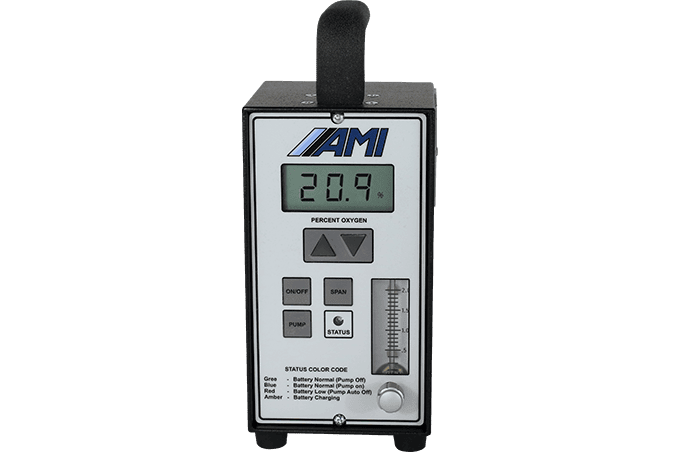
MODEL 111
The Importance of Monitoring Atmosphere Gases in Industrial Applications
Monitoring atmosphere gases is vitally important in many industrial processes. Sectors that rely on this monitoring include the aerospace and automotive industries and steel manufacturers. Common examples include steel mill gas monitors and gas measurement in heat treatment furnaces used to ensure components meet strict specifications.
The importance of monitoring atmosphere gases extends to multiple aspects of these industrial processes.
Process optimization
Monitoring ensures that the proper composition of gases is present to promote product quality, maintain efficient operations, and reduce energy consumption.
Protecting equipment and process integrity
Monitoring for harmful levels of gases can help prevent equipment corrosion, resulting in improved lifespans and reduced operational downtime.
Safety and risk management
Continuous gas monitoring can detect health and safety risks caused by inadequate levels of oxygen for humans. Timely detection of abnormal conditions prevents exposure to unsafe environments minimize accidents and protect the workforce.
Regulatory compliance
Compliance with environmental regulations is imperative in many industries. Monitoring promotes compliance so companies can avoid legal issues and fines while promoting operational safety.
Use Cases of AMI Products
in Heat Treatment Applications
Many companies use AMI products to perform a range of gas measurements in heat treatment. Following are some examples of AMI products and industries in which they are currently deployed.
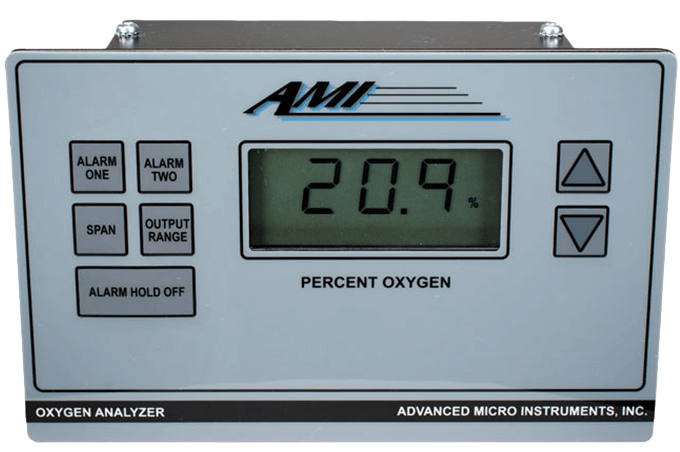
Percent Oxygen Analyzer MODEL 70
The MODEL 70 is a panel-mounted percent oxygen analyzer that accurately measures in a non-flammable gas stream. The device is suitable for general-purpose environments and provides accurate and stable reading over a wide O2 measurement and temperature range. Companies using the MODEL 70 include materials and autoclave manufacturers for monitoring oxygen levels during heat treatment.
Another common application for the MODEL 70 is to measure oxygen levels in the enclosed environment of heat treatment equipment post-operation. Safety measures are programmed such that the equipment will not open until the MODEL 70 reads oxygen levels are safe for humans.
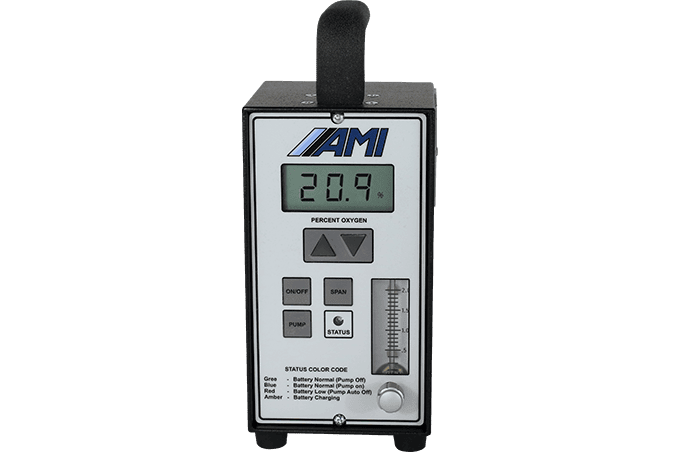
Portable Percent Oxygen Analyzer MODEL 111
The MODEL 111 portable percent oxygen analyzer is ideal for monitoring oxygen measurements in non-flammable gas samples. It is a versatile monitoring solution available in three configurations to fit diverse usage scenarios. An aerospace company currently uses this analyzer to spot-check oxygen levels in an atmospheric furnace.
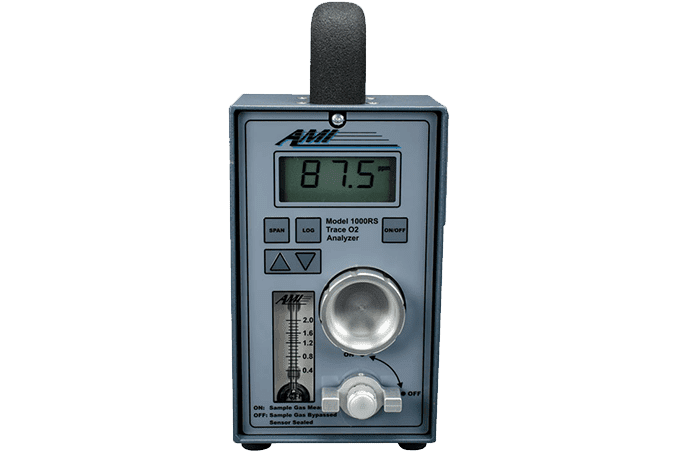
Portable Trace Oxygen Analyzer MODEL 1000RS
The MODEL 1000RS provides customers with a portable trace oxygen analyzer in flammable gas environments. Patented technology guarantees fast and reliable O2 measurement. Data logging functionality facilitates identifying difficult-to-locate intermittent leaks in the field. This industry-leading analyzer is used by a nanoparticle company to monitor heat treatment operations.
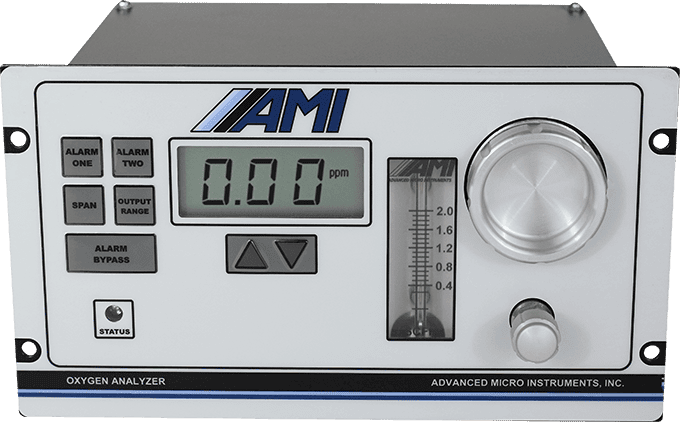
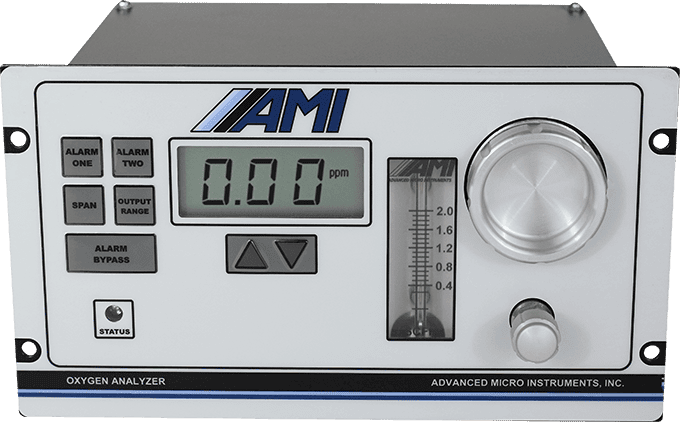
Trace Oxygen Analyzers MODEL 2001RS and MODEL 2001RSP
The MODEL 2001RS family of analyzers are advanced trace oxygen analyzers that deliver accurate, reliable, and rapid response times in a panel mounted, virtually maintenance-free package. The 2001RS provides positive pressure sampling and the 2001RSP is able to continuously monitor processes when conditions are at atmospheric pressure or in vacuum. The analyzers include two fully adjustable concentration alarms offering configurable alarm logic and relay contacts. Data logging capabilities provide information for troubleshooting and optimizing performance.
The 2001RS is currently used by a battery manufacturer in its annealing process. Examples of use cases employing the 2001RSP include aerospace companies using the device for annealing in a tunnel oven and heat treatment furnaces. A plasma processor is leveraging the capabilities of the 2001RSP to monitor oxygen levels during the metal additive process.
Another customer recently deployed a 2001RSP because of its capability to measure lower O2 levels than their previous solution. The company performs annealing in an argon environment and will benefit from the continuous monitoring provided by the 2001RSP. Our excellent customer service during the selection phase was another reason this organization chose to go with AMI.
Understanding Gas Analyzers for
Heat Treatment
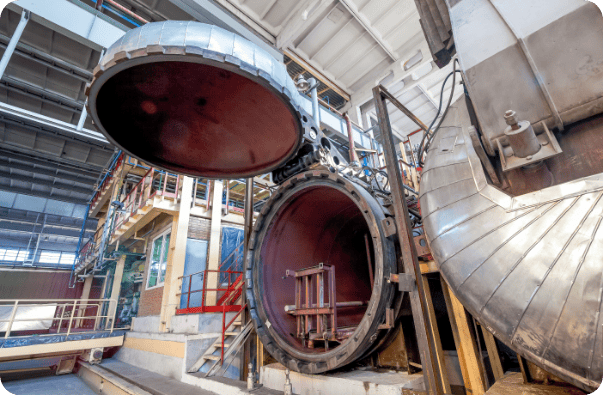
Gas analyzers are specialized instruments that assess specific gases in the process environment of materials going through a heat treatment process. The processes, such as annealing, tempering, quenching, and nitriding, alter the microstructure of metals and alloys to improve their mechanical properties. The devices come in various form factors and configurations that address different industrial requirements.
Continuous gas analyzers provide organizations with a constant view of the industrial process environment and data that can be instrumental in optimizing procedures. Portable gas analyzers furnish flexibility and versatility to handle unexpected operational issues. A gas analyzer for heat treatment furnaces supplies information critical for operational efficiency and safe operation.
Gas measurement in heat treatment furnaces is necessary to verify that processes are consistent and produce the desired properties in treated materials. Specific benefits of gas measurement include:
- Composition monitoring to control the atmosphere and obtain optimal results
- Controlling oxygen levels to prevent unwanted oxidation
- Ensuring safe levels of oxygen to support worker safety pre- and post- treatment operation
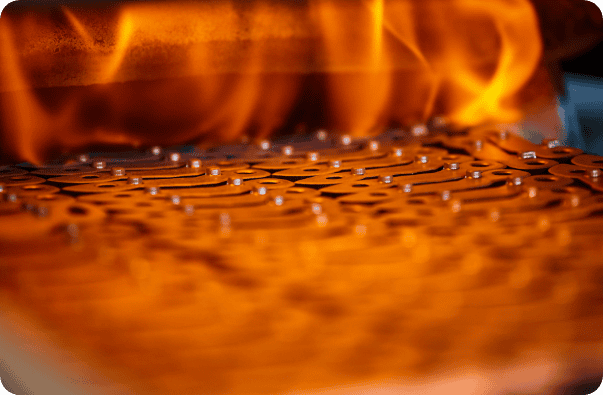
Ensuring Safety with Heat Treatment and Autoclave Operations
Safety is a critical consideration in the heat treatment and autoclave equipment chambers as well as the surrounding environments where this equipment is installed. The safety promoted by gas analyzers in these operations is vital for multiple reasons. AMI’s analyzers address the specific safety concerns related to oxygen deficiency.
Heat treatment is often performed in oxygen deficient environments for optimal results. These oxygen deficient environments are created by introducing nitrogen, argon, or other inert gases to the treatment vessel. These inerting gases are stored in pressurized gas cylinders or as liquefied gases in dewars, both which have the potential to leak. As these inerting gases can displace oxygen in air, there is the risk of asphyxiation if a human is in the area where a gas leak occurs. Therefore, it is important to monitor the environment where these inerting gases are stored. In the U.S. and other countries, there are regulatory requirements to monitor such environments to maintain a safe workplace. AMI’s MODEL 221R Oxygen Deficiency Monitor will monitor the environment for safe oxygen levels and generates an alarm if oxygen deficient levels are detected.
Oxygen Deficiency
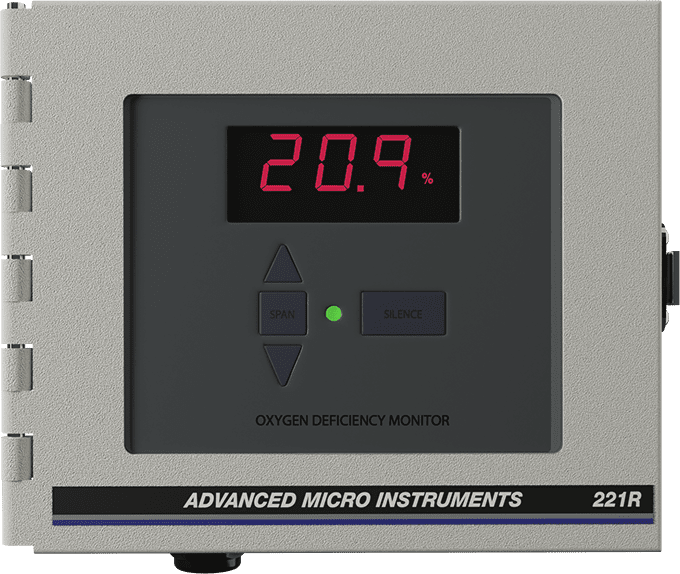
MODEL 221R
Safety in the heat treatment process has been improved by advanced solutions such as those offered by AMI’s MODEL 70 and MODEL 2001RS/RSP. Following are some technical advancements that differentiate these advanced analyzers and make them more effective in addressing industrial concerns.
- Gas analyzers for safety compliance provide real-time monitoring and alerts. Alarms attached to continuous oxygen analyzers for safety can be responsible for alerting personnel of dangerous conditions so they can take preventative action. Both the MODELS 70 and 2001RS/RSP provide real-time monitoring and adjustable alarms.
- Analyzers promote safety by supplying information critical to avoiding asphyxiation in oxygen depleted environments. As the operational environment of large heat treatment vessels are typically deficient in oxygen for process optimization, it is necessary to exhaust the argon and nitrogen used to create the oxygen deficient environment and reintroduce air into the chamber once the treatment process is complete. AMI’s MODEL 70 is used to ensure an exhausted chamber has a safe level of oxygen present before the vessel is opened.
- Robust construction of all AMI analyzers ensures the long-term viability of an analyzer and its continued effectiveness in industrial processes.
Trace Oxygen Monitoring
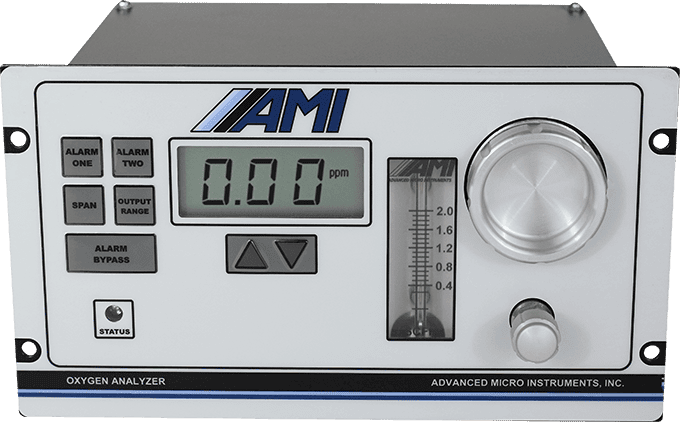
MODEL 2001RS/RSP
Percent Oxygen Monitoring
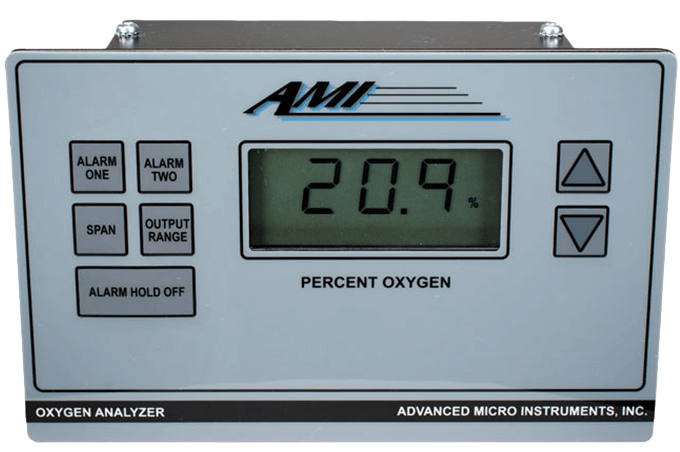
MODEL 70
Specialty Analyzers for Metal Finishing and Treatment
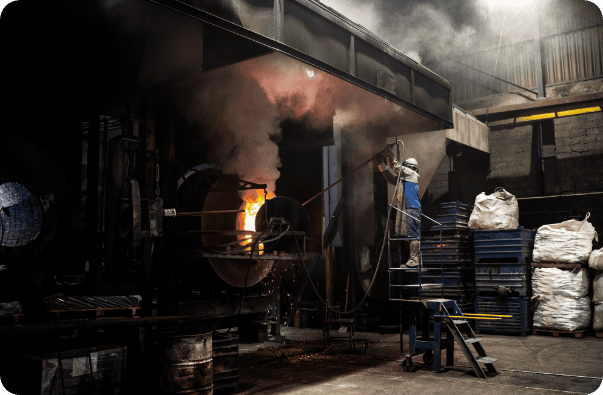
Specialty gas analyzers are available to address specific needs in certain industries. Examples of specialty analyzers include gas analyzers used in metal finishing and gas analyzers used for titanium treatment.
Benefits of utilizing industrial gas analyzers for specialized metal treatment include:
- Improving process control with continuous monitoring of the treatment environment
- Enabling improved quality by reducing defects by ensuring a consistent process environment
- Saving energy and reducing costs through increased efficiency of a tightly controlled treatment environment
- Supporting worker safety by monitoring the working environment for unsafe oxygen levels
Gas analyzers for heat treatment play an important role in many industries. They provide companies with the information they need to ensure the safe and optimal operation of industrial equipment such as ovens, autoclaves, and furnaces. Worker safety and customer satisfaction are both promoted through the use of gas analyzers for heat treatment processes.
AMI’s advanced permanent mount and portable analyzers offer customers flexible solutions for enhanced process control, environmental safety, and product quality. Our products are designed and constructed to provide the information your company needs to operate heat treatment equipment safely, effectively, and efficiently.
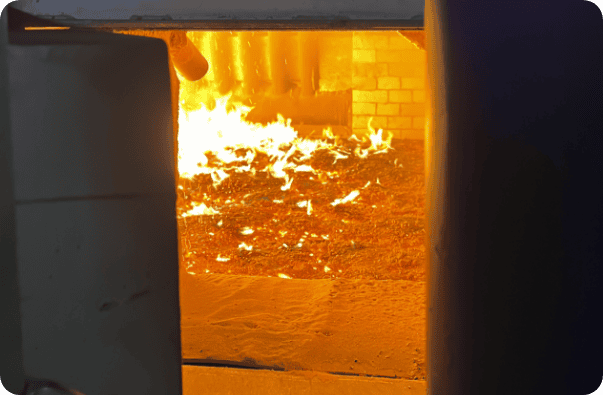