Air separation units (ASUs) are vital to produce oxygen, nitrogen, argon and other gases needed in many processes across a wide spectrum of industries. Gas quality and purity is essential for maintaining safety and operational efficiency. It may also be necessary to achieve compliance with governmental and industry standards.
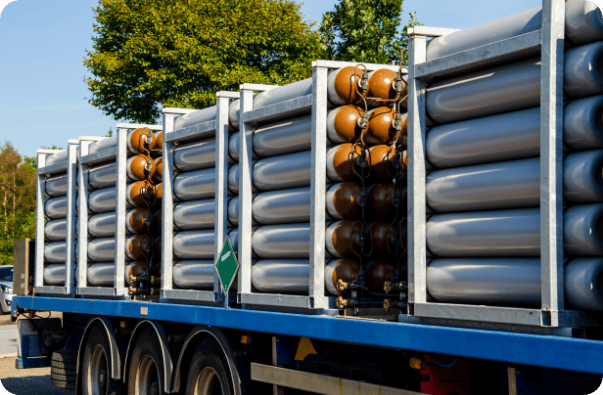
Diverse industries such as manufacturing, energy production, and healthcare rely on the consistent supply of quality gas for industrial processes or patient care. Variable purity levels are typically unacceptable and can lead to downtime and lost productivity. Inaccurate measurements can result in dangerous conditions for workers and compromised product quality.
AMI offers customers high-quality gas measurement equipment designed to meet your unique operational requirements. Our oxygen analyzers and deficiency monitors furnish the accurate information you need to optimize your ASU systems. Learn more about ASUs and the AMI equipment designed to optimize their performance and keep your employees safe.
Popular Products for ASUs
The following AMI products are popular for use with air separation units.
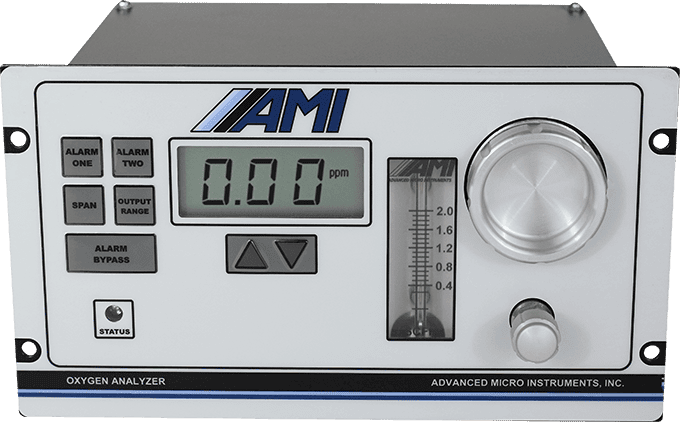
Trace Oxygen Monitoring MODEL 2001RS/RSP
The model 2001RS/RSP is a trace oxygen analyzer that facilitates easy oxygen measurement. The panel-mounted unit features a compact design and AMI’s patented eliminator cell block and trace oxygen sensors. Accurate, reliable, and fast response times are delivered by this virtually maintenance-free unit.
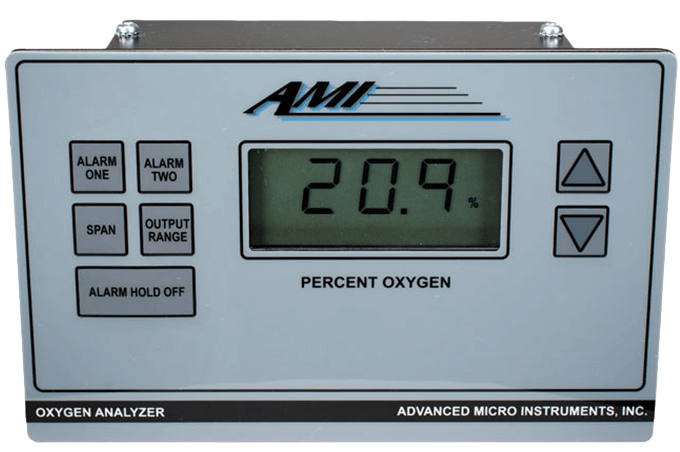
Percent Oxygen MonitoringMODEL 70
AMI’s most advanced percent oxygen analyzer is best in class and the preferred choice of engineers and measurement technicians. Its superior design and patented technologies deliver cost-effective and reliable performance.
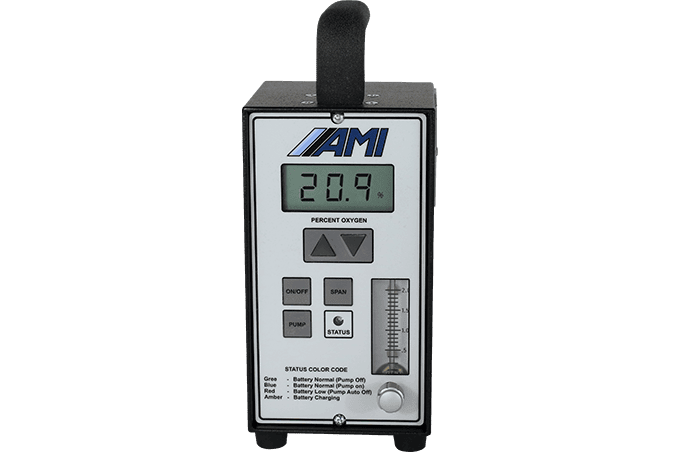
Percent Oxygen MonitoringMODEL 111
The Model 111 is a portable percent oxygen analysis solution for use with non-flammable gases. The device features a long-life zirconium oxide sensor to deliver stable readings even with temperature or barometric pressure changes. Customers can choose from three configurations to fit their specific analysis needs.
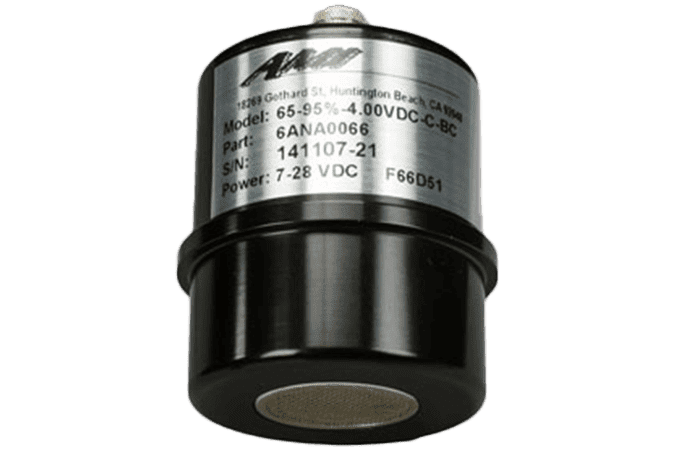
Percent Oxygen MonitoringMODEL 65
The Model 65 is an affordable, general purpose percent oxygen analyzer for non-flammable gases. It functions as a standalone sensor and utilizes zirconium oxide sensor technology to deliver reliable readings despite temperature or barometric changes.
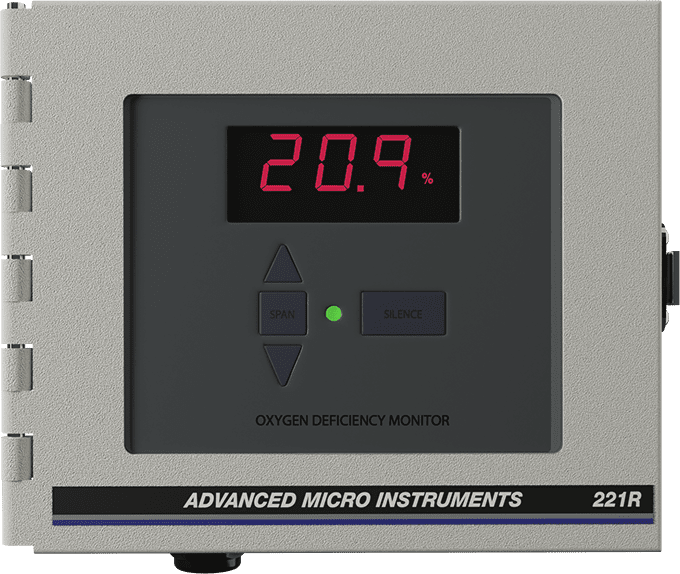
Oxygen DeficiencyMODEL 221R
This oxygen deficiency monitor is designed for safety. It is virtually maintenance-free and delivers a 10-year life expectancy with its unique oxygen sensor. The unit provides accurate and stable readings over a wide temperature range. Thousands of Model 221R units are used in U.S. Government labs, universities, and industries to ensure personnel safety. This device should not be used in areas where flammable gas may be present.
Understanding
Air Separation Units
An air separation unit is a system that separates air into its primary components. Atmospheric air is typically separated into oxygen, nitrogen, and argon for use in industrial processes. While ASUs may use different separation techniques, they share common functions and components.
ASU functions and components
Air separation units utilize multiple stages and perform several key functions to accomplish their goal.
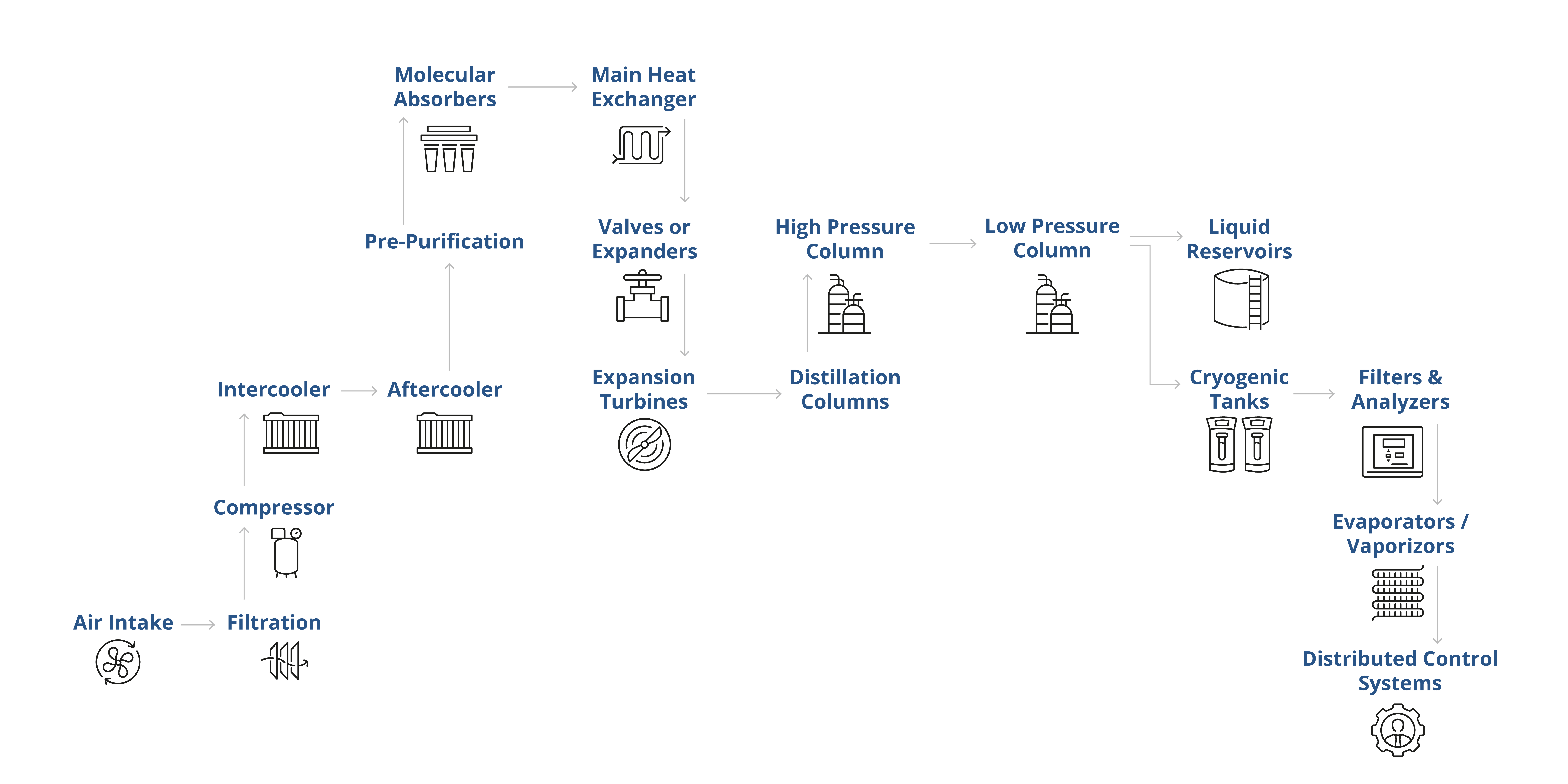
- Air intake - The first step in an ASU is to draw air into the unit so it can be separated. Dust is filtered out of the air before it is sent to the compression stage.
- Compression - After the air is filtered, it is compressed to increase its pressure. Compression is necessary for the cooling and separation processes.
- Purification - The compressed air may be purified to remove moisture, carbon dioxide, or other gas or chemical impurities. Purification ensures the high purity of the separate gases and mitigates potential problems affecting the cryogenic equipment.
- Cooling - The compressed air needs to be cooled if cryogenic distillation will be used to separate its components. This is typically done with a series of refrigeration cycles and heat exchangers. The air is liquefied for the distillation process which is based on the different boiling points of the different components in the compressed air.
- Separation - Separation is performed using either cryogenic distillation or non-cryogenic methods. We will look at these options in more detail in the next section.
- Recovery - The separated gases are collected for use in industrial processes. Nitrogen is usually produced in higher volumes than oxygen or argon. The gases can go through additional purification processes if necessary for a specific application.
- Storage and distribution - After purification, the gases may be stored in their gas or liquid state in tanks for transfer to other locations. Distribution can be provided directly to end-users with gases fed into industrial processes or equipment.
Types of air separation units
The air separation phase can employ multiple techniques. These methods are vastly different and may be used to address varying usage scenarios.
- Cryogenic distillation - Cryogenic distillation requires air to be cooled to very low temperatures. Cryogenic typically indicates temperatures below 120 degrees Kelvin or more than -243 degrees Fahrenheit. After cooling, the air is expanded in a distillation column where components are separated based on their different boiling points. For example, nitrogen liquefies at a lower temperature than oxygen. This type of ASU can produce oxygen with a purity of up to 99.5%.
- Pressure swing adsorption (PSA) - PSA is a non-cryogenic air separation method utilizing absorbent materials to absorb nitrogen from compressed air. The cycle-based process swings the absorbent material from high to low pressure. The absorbed nitrogen is released to enable the production of purified oxygen. PSAs produce lower purity oxygen, typically from 90 to 95% pure. They are often used in smaller operations or in locations that cannot support cryogenic units.
- Membrane separation - This non-cryogenic technique uses membrane technology that employs selection permeation to separate gases according to chemical properties of molecule size. A specially designed membrane separates air components based on how quickly specific gases pass through it. This method can produce oxygen or nitrogen without cryogenics and offers an energy-efficient and compact solution for small operations.
- Vacuum pressure swing adsorption (VPSA) - VPSA operates similarly to PSA separation. It employs a vacuum which allows oxygen production at lower pressures than the PSA method.
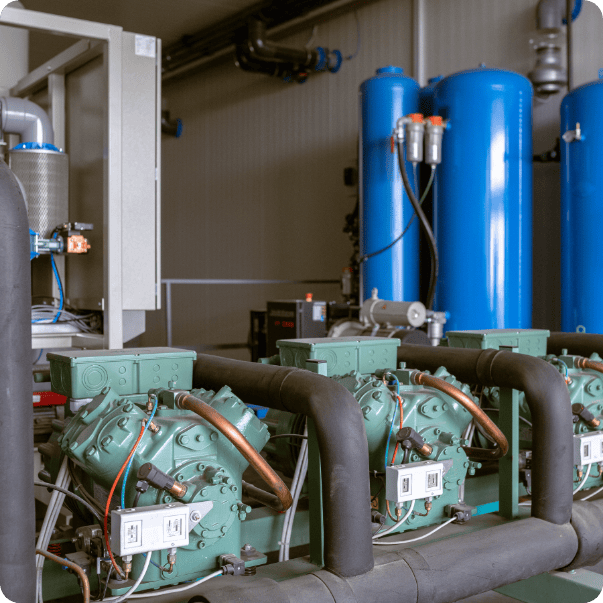
Industrial applications of air separation units
Many industries utilize ASUs to generate essential gases for multiple uses. ASUs enable organizations to produce industrial gases at a lower cost than buying them on the open market. ASU use ensures a consistent and reliable supply of gases for critical operations while minimizing transportation and storage costs. Units can be manufactured to address the specific requirements of different industries and processes.
Following are some of the industries that manage their own gas generation with on-site ASUs.
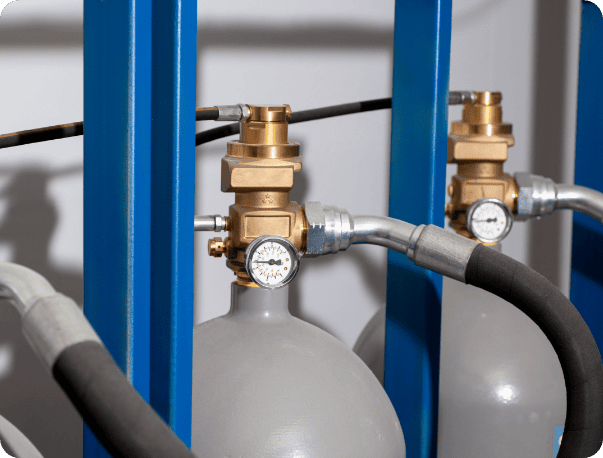
- Manufacturing - ASUs are used in many processes in industries like steel, chemical, and petrochemical manufacturing. Large volumes of oxygen and nitrogen are required for these processes.
- Healthcare - ASUs are vital for producing oxygen for patient treatment in the healthcare sector. Impurities can be extremely detrimental for patient well-being and need to be avoided at all costs.
- Energy production - Oxygen and nitrogen are essential for multiple energy generation processes such as combustion and purging during energy production. Consistent access to these gases enables smooth energy production for business and residential use.
- Semiconductor and electronics - Very pure nitrogen and argon are required in the production of electronic components and semiconductor chips. Impurities may cause contamination and lead to inferior products.
- Food and beverage - The food and beverage industry uses nitrogen and carbon dioxide for refrigeration and packaging to preserve freshness during shipping.
Gas Generators:
On-Site Gas Production
On-site gas generators enable businesses that consume large volumes of industrial gases to produce these vital resources at the point of use. Organizations utilizing ASUs for on-site gas generation can expect to enjoy the following benefits.
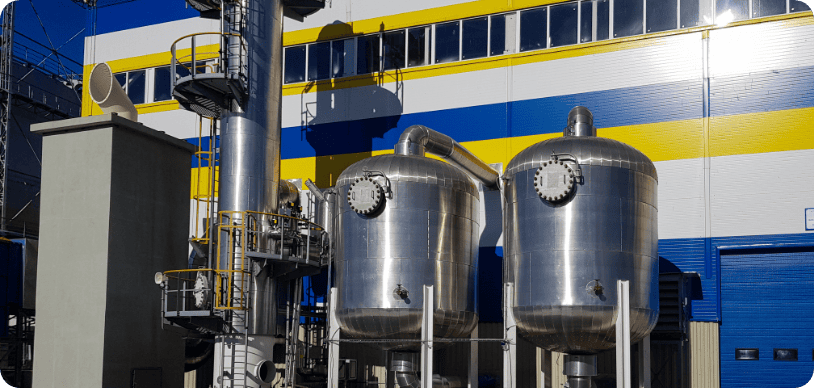
Flexibility and control
On-demand gas generation enables a company to tightly control production to address fluctuating business requirements. On-site generation systems can be customized to produce gases at specific purity levels and flow rates. Generation can be configured for specific applications such as in the medical establishment or semiconductor manufacturing sector. Companies can generate the precise amount of gas needed and avoid waste and overproduction.
Cost-effective solutions
Generating gas on-site can reduce costs in multiple ways.
- Costs are reduced by self-production of the required resources rather than purchasing gases from a third party.
- Companies can protect themselves from market price fluctuations with an on-site solution.
- Transportation of gases to operational locations is minimized.
- On-site gas production eliminates the majority of storage costs.
Reduced environmental impact
Reducing an organization’s environmental impact is another benefit of on-site gas generation.
- Lowering its carbon footprint is good for the environment and can generate positive public relations for a company.
- Eliminating the need to transport gases helps organizations reduce their carbon footprint.
- On-site gas generation equipment may leverage renewable energy sources to promote sustainability.
- Controlling production via on-site generation reduces waste and may use raw materials more efficiently.
Supply reliability
On-site gas generation ensures a reliable supply to maintain productive operations. Companies don’t need to worry about supply chain disruptions that may impact the business. This is an vitally important factor for companies requiring a high-steady demand of gases or performing time-sensitive processes.
The Importance of Gas Quality in ASUs
The quality and purity of gases generated in an ASU is important for multiple reasons.
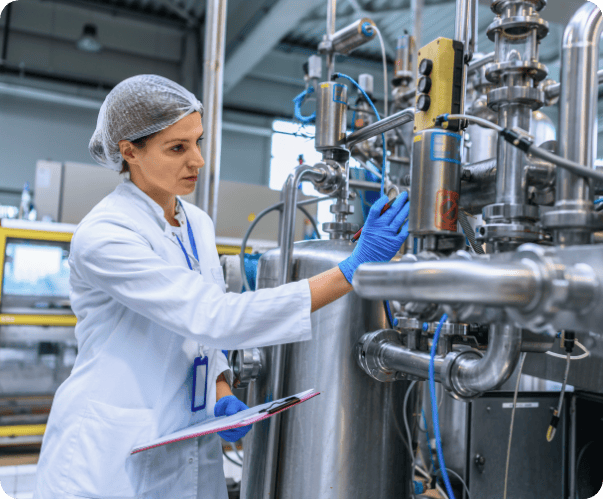
Impact on industrial processes
Gas purity affects product quality and the operational efficiency of industrial processes.
- Product quality - Impurities in gas can result in defects, contamination, or unexpected reactions that degrade product quality. Consistency and performance often relies on the ability to ensure the use of high-quality gases. Fields such as healthcare, pharmaceutical production, food processing, and manufacturing require quality gases.
- Operational efficiency - High purity gases are essential for optimizing reactions, reducing downtime, and extending equipment life. Impure gases may result in excessive maintenance costs and inefficiencies such as increased energy use. Purity supports a cost-effective production environment and operational efficiency.
Safety and regulatory compliance
Producing quality gas by ASUs is essential to maintain safety and meet regulatory requirements.
- Product safety and purity - Proper gas purity minimizes the chances of explosions or unexpected reactions that can compromise product safety and put workers at risk. Purity is vital in medical applications to ensure safe patient treatment.
- Operational safety - Employee safety is promoted by ensuring sufficient oxygen concentrations to prevent dangerous working conditions. Alerts are generated by the model 221R when oxygen levels are not safe for humans.
- Regulatory compliance - Gas purity is necessary to comply with national and international safety, environmental, and industry-specific regulations. Non-compliance can result in fines and damage the organization’s reputation. Emission thresholds are also easier to meet when using purified gases to meet environmental regulations. Purity standards help protect a company from legal issues with employees, consumers, or patients.
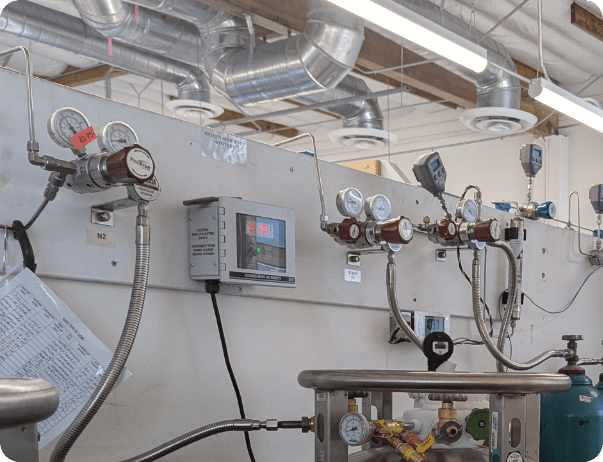
Advanced Gas Measurement Equipment
AMI’s innovative gas measurement solutions contribute to operational efficiency and enable you to optimize your ASU system production. Our equipment includes the following products and features.
High-Precision Gas Analysis
We manufacture high-precision gas analyzers that provide accurate measurements for effectively monitoring gas composition. We employ advanced technology to ensure your readings are always correct under variable temperatures and barometric conditions.
Real-Time Monitoring
Our real-item monitoring systems provide you with the data you need to make informed decisions regarding your ASU systems. They enhance process control and give you the information needed to optimize production and maintain safety.
Customizable Integration
AMI builds its equipment with excellent integration capabilities, as they can be used with your existing ASU systems. We streamline the process of implementing AMI products into your current ASU environment.
Benefits of Implementing AMI Equipment
AMI’s advanced measurement equipment will elevate the performance of your ASU. Our products provide multiple benefits that help your company maintain operations and provide your customers with high quality products.
Superior gas purity levels
Achieving and maintaining high levels of gas purity is essential. Our advanced technology helps you ensure the correct purity for your requirements. We discuss the engineering that goes into our products and separates us from the competition in a subsequent section of this article.
Enhanced operational efficiency
Our equipment is manufactured to be durable and maintain accuracy throughout its lifetime. We strive to reduce your downtime and increase throughput to enhance operational efficiency.
Cost savings and ROI
Investing in advanced measurement technology typically results in long-term cost-savings. A considerable return on investment is achieved through the consistent and reliable performance of our equipment.
Case Studies
The following examples highlight the proven success organizations have enjoyed by implementing AMI’s advanced technical solutions.
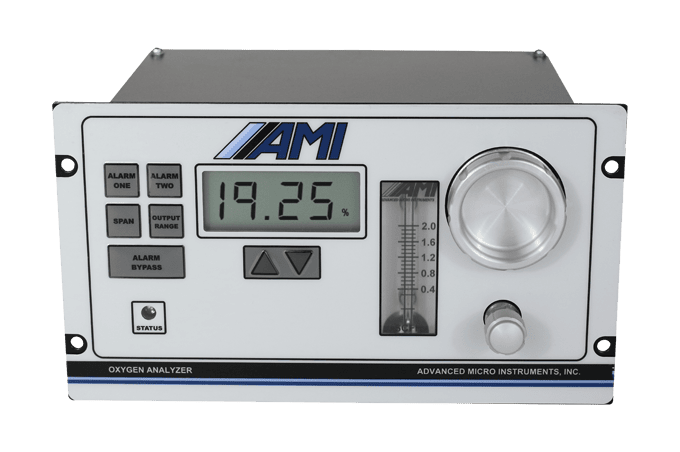
MODEL 201RS
A manufacturer of oxygen production systems used in water treatment, medical, and industrial processes utilizes AMI models 201RS and 65 to monitor oxygen concentration.
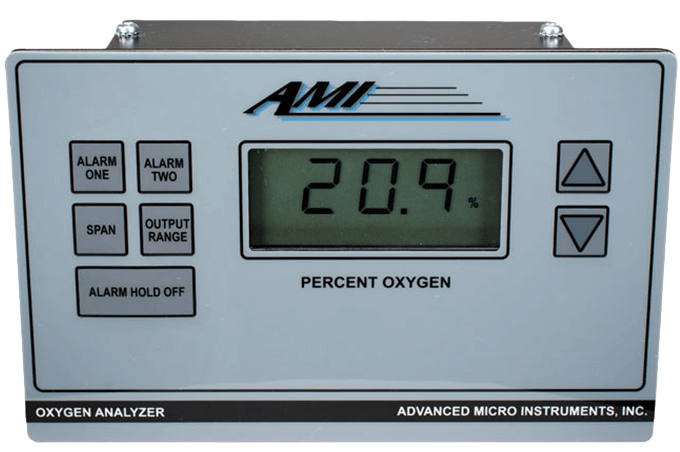
MODEL 70
An oxygen generation product manufacturer focused on maritime and aviation applications measures percent oxygen levels with the AMI model 70.
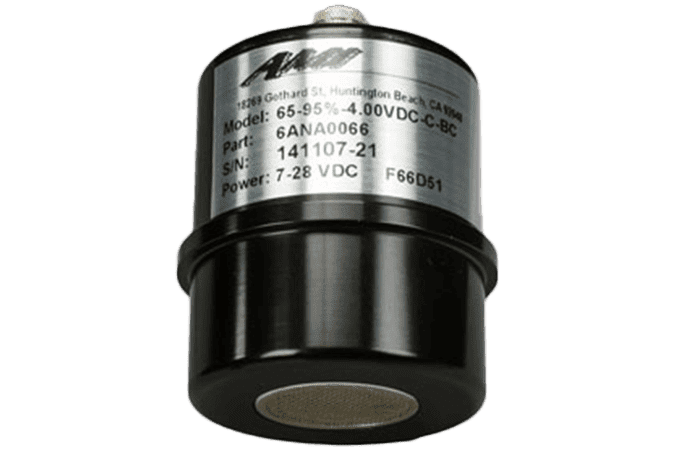
MODEL 65
A residential oxygen enrichment company purchases AMI’s model 65 for reliable oxygen measurement.
A company manufacturing adsorption-based oxygen production equipment employs the AMI model 65.
The Engineering Behind Our Equipment
AMI’s engineering sets it apart from competitors in the ASU manufacturing field. Our advanced engineering results in reliable products that are easy to use.
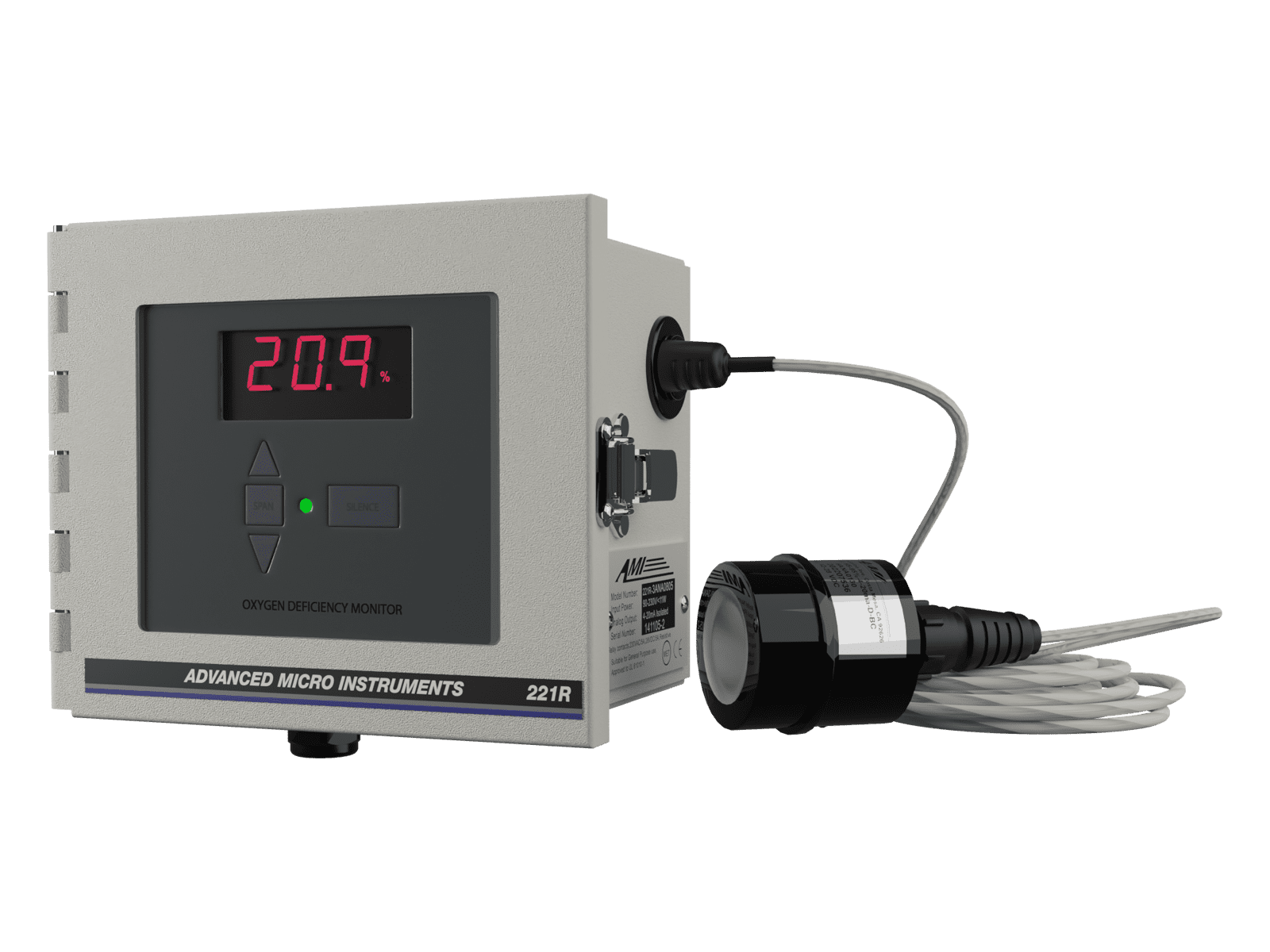
Cutting-edge sensor technology
Our proprietary sensor technology provides customers with accurate and reliable measurements. Patented sealing technology eliminates leaks and extends the sensor’s useful life. Oxygen is diffused through a unique membrane so it is immediately reduced at the cathode. We have perfectly positioned the anode and cathode to produce fast response times, high stability, and linear outputs that outperform competitors. All sensors are performance-tested over multiple temperature ranges to meet our high-quality standards.
User-friendly interfaces
Our equipment features a powerful Command Center User Interface. This user-friendly interface streamlines operation and monitoring by your technical team. Technicians can use the interface to configure and troubleshoot any AMI gas analyzer. Variable types of alarms can be set to ensure safe and consistent ASU operation. The software can generate time-stamped data logs for use in solving intermittent issues with the equipment.
Unique eliminator cell block technology
Our unique patented eliminator cell block offers a unique sample system approach that virtually eliminates all potential leak paths and optimizes flow efficiencies. The compact sample system and flow efficient sensor pocket are built directly into a solid metallic block. We eliminated long lengths of tubing which can leak with precision drilled intersecting gas passages. The cell block delivers up to 400% faster measurement response time and minimizes the size of the analyzer.
Seamless system integration
Our systems are designed to seamlessly integrate with various control systems and software platforms. The addition of our equipment augments the capabilities of your current ASU environment. The information provided by AMI’s devices improves production and promotes safety in industries utilizing air separation units.
Air Separation Downloads
We also have an extensive literature library that provides customers with detailed information about gas production and our wide range of products.
Getting Started
Optimize your air separation unit today with the addition of one of AMI’s line of gas measurements devices. Talk to a specialist at AMI today and request a quote for the equipment that will enhance your ASU system.